Primer for Self-leveling Concrete Overlays
Paramol is a premium-grade vinyl acetate primer specifically designed for self-leveling concrete flooring applications. It provides maximum adhesion and seal between the substrate and overlay..
Paramol is part of our Param self-leveling concrete flooring system. Param Self-leveling Concrete is used to achieve durable and decorative flooring outcomes in commercial, business, and residential projects.
Param and Paramol can be used over new or old concrete, plywood and more. Param and paramol are used in the installation of heated concrete and in residential homes over plywood.
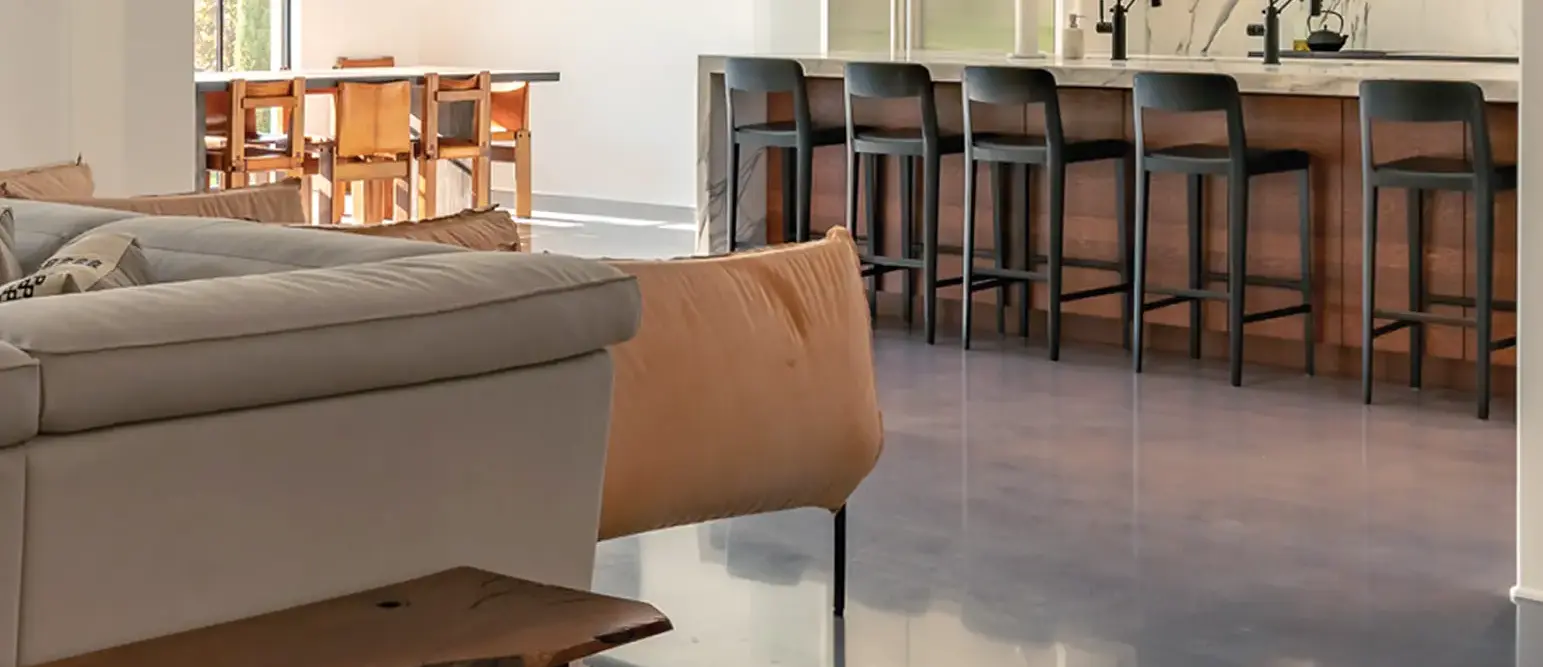
Features
- Water-based and VOC compliant
- Odorless, can be used in occupied spaces
- Non-flammable, non-toxic, non-explosive
- Creates an excellent bond
- High solids content
Installation
Shown at the right is Paramol being used as a primer for a concrete overlay installation being applied over a residential plywood floor substrate.
Please read the technical data shoot, or consult a Duraamen representative for detailed instructions.
- Paramol must be applied over entire substrate that is at least at 50°F
- For porous substrates 2 coats of Param primer may be necessary.
- The primer is dilution @ 1:1 with clean potable water before applying on the surface.
- The primer must be applied evenly with a fine hair push broom. DO NOT use paint rollers, mops, or spray equipment except over wood and metal
- Apply a thin primer layer leaving no bare spots, puddles or excess primer. Allow to dry to a clear, thin film.
- Important: The concrete overlay must be applied within 24 hours of priming to insure that a good bond is achieved between primer and the substrate. It is very important that the primed substrate is not contaminated in any way prior to the installation of the overlay.
What are the main benefits of polyaspartic coating?
The main benefits of polyaspartic coating include its fast drying time, durability, and chemical resistance. It is also eco-friendly and can be applied year-round.
How does polyaspartic coating compare to epoxy?
Polyaspartic coating dries faster and offers better UV stability compared to epoxy. It is also more durable and resistant to chemicals, making it a superior choice for many applications.
Can polyaspartic coating be applied in any weather?
Yes, polyaspartic coating can be applied in a variety of weather conditions, including extreme temperatures. This makes it a versatile option for different climates.
What should I do if my polyaspartic coating starts to fade?
If your polyaspartic coating starts to fade, consider applying a UV-stable topcoat. Regular maintenance and cleaning can also help preserve the color.