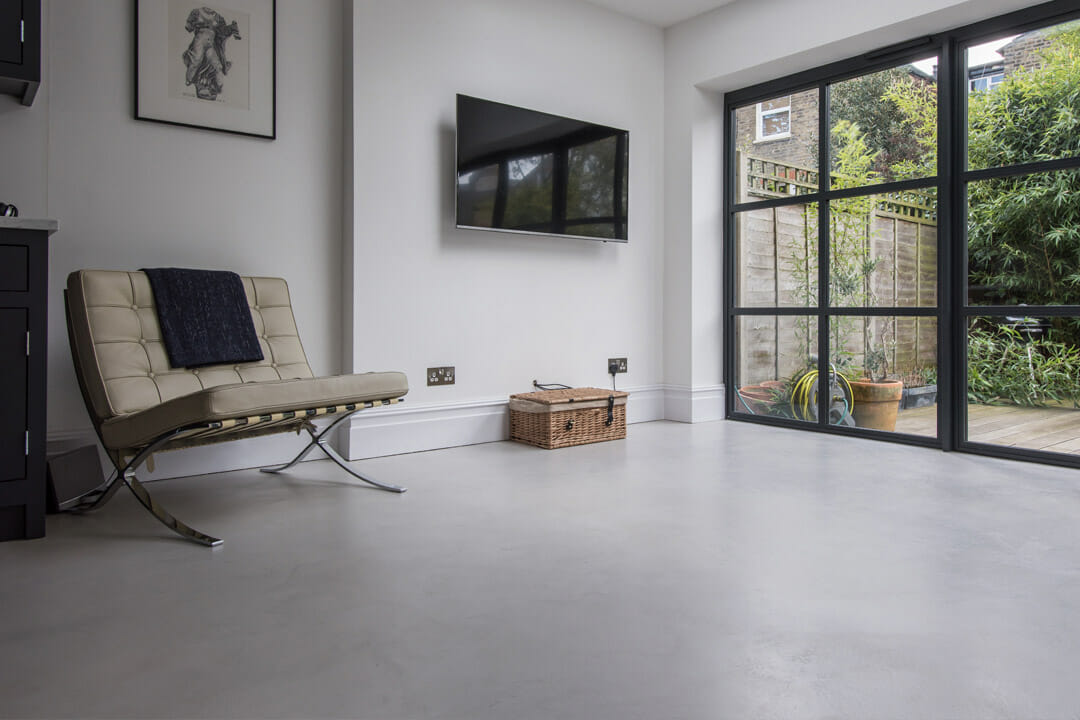
How Does It Works?
Polyaspartic coating works by creating a chemical reaction between the polyisocyanate and the polyaspartic ester. This reaction forms a strong, flexible, and durable layer that adheres well to various surfaces. The coating can be applied in multiple layers to achieve the desired thickness and finish.
- Chemical Reaction: Ensures a strong bond and quick curing.
- Multiple Layers: Allows for customization of thickness and finish.
Common Applications
Polyaspartic coatings are used in a variety of settings due to their durability and fast-curing properties. Common applications include:
- Garage Floors: Provides a durable and easy-to-clean surface.
- Industrial Floors: Resistant to chemicals and heavy traffic.
- Outdoor Spaces: UV stable and weather-resistant.
Pros and Cons of Polyaspartic Flooring
The Pros of Polyaspartic Flooring
Long-Lasting
Polyaspartic flooring is known for its longevity. It can withstand heavy traffic and harsh conditions without showing signs of wear and tear.
- Durability: Lasts longer than many other types of flooring.
- Low Maintenance: Requires minimal upkeep.
Fast Drying
One of the standout features of polyaspartic coating is its fast drying time. This allows for quicker project completion and less downtime.
- Quick Curing: Dries in a matter of hours.
- Reduced Downtime: Projects can be completed faster.
Eco-Friendly
Polyaspartic coatings are considered eco-friendly due to their low VOC (Volatile Organic Compounds) content. This makes them a safer choice for both installers and the environment.
- Low VOC: Reduces harmful emissions.
- Environmentally Safe: Better for the planet.
Resistant to Chemicals
Polyaspartic coatings are highly resistant to chemicals, making them ideal for industrial and commercial settings where spills and exposure to harsh substances are common.
- Chemical Resistance: Withstands exposure to various chemicals.
- Ideal for Industrial Use: Suitable for factories and warehouses.
Year-Round Installation
Unlike some coatings that require specific temperature conditions, polyaspartic coatings can be applied year-round, making them a versatile option for various climates.
- All-Weather Application: Can be installed in any season.
- Versatile: Suitable for different climates.
The Cons of Polyaspartic Flooring
Limited Color Options
One of the drawbacks of polyaspartic flooring is the limited color options available. This can be a disadvantage for those looking for a specific aesthetic.
- Color Limitations: Fewer choices compared to other coatings.
- Aesthetic Constraints: May not match all design preferences.
More Expensive
Polyaspartic coatings tend to be more expensive than other types of flooring, such as epoxy. This can be a consideration for budget-conscious projects.
- Higher Cost: More expensive upfront.
- Budget Considerations: May not be suitable for all budgets.
Slippery
When wet, polyaspartic flooring can become slippery, posing a potential safety hazard. This is something to consider, especially in areas prone to moisture.
- Slippery Surface: Can be hazardous when wet.
- Safety Concerns: Requires additional measures for slip resistance.
Polyaspartic Coating vs. Epoxy
Drying Time
Polyaspartic coatings have a significantly faster drying time compared to epoxy. This allows for quicker project completion and less downtime.
- Polyaspartic: Dries in a few hours.
- Epoxy: Takes several days to cure.
Durability
Both polyaspartic and epoxy coatings are durable, but polyaspartic tends to have a longer lifespan and better resistance to wear and tear.
- Polyaspartic: Longer-lasting and more resilient.
- Epoxy: Durable but may require more maintenance.
UV Stability
Polyaspartic coatings offer superior UV stability, making them ideal for outdoor applications where exposure to sunlight is a concern.
- Polyaspartic: UV stable and resistant to yellowing.
- Epoxy: Prone to yellowing and degradation under UV light.
Common Problems with Polyaspartic Coatings
Problem #1: Bonding Issues with Concrete
Bonding issues can occur if the concrete surface is not properly prepared before applying the polyaspartic coating. This can lead to peeling and poor adhesion.
How to Avoid Bonding Issues
To avoid bonding issues, ensure that the concrete surface is clean, dry, and free of contaminants. Proper surface preparation is key to a strong bond.
- Surface Preparation: Clean and dry the concrete thoroughly.
- Contaminant Removal: Ensure no oils or debris are present.
Problem #2: Air Bubbles in the Coating
Air bubbles can form in the polyaspartic coating if it is applied too quickly or if the surface is not properly prepared.
How to Avoid Air Bubbles
To prevent air bubbles, apply the coating slowly and evenly. Make sure the surface is smooth and free of imperfections.
- Slow Application: Apply the coating at a steady pace.
- Smooth Surface: Ensure the surface is even and clean.
Problem #4: Improper Mixing Ratios
Improper mixing ratios can lead to a weak or ineffective coating. It’s crucial to follow the manufacturer’s instructions precisely.
How to Ensure Proper Mixing
To ensure proper mixing, use the exact ratios specified by the manufacturer. Mix thoroughly to achieve a consistent blend.
- Follow Instructions: Adhere to the manufacturer’s guidelines.
- Thorough Mixing: Ensure a uniform mixture.
Problem #5: Fading Over Time
Fading can occur if the polyaspartic coating is exposed to harsh UV rays without proper UV stabilizers.
How to Prevent Fading
To prevent fading, choose a polyaspartic coating with UV stabilizers. Regular maintenance can also help preserve the color.
- UV Stabilizers: Opt for coatings with UV protection.
- Regular Maintenance: Keep the surface clean and well-maintained.
Is Polyaspartic Coating Right for You?
Factors to Consider
When deciding if polyaspartic coating is right for you, consider factors such as budget, application environment, and desired aesthetics.
- Budget: Assess if the cost fits within your budget.
- Environment: Consider the conditions where it will be applied.
- Aesthetics: Determine if the available colors and finishes meet your needs.
Ideal Use Cases
Polyaspartic coatings are ideal for a variety of applications, including residential, commercial, and industrial settings.
- Residential: Perfect for garage floors and patios.
- Commercial: Suitable for retail spaces and showrooms.
- Industrial: Ideal for factories and warehouses.